Oscillating Bearings: Solutions for Every Industry
Oscillating bearings play a crucial role in many industries, ensuring smooth and reliable oscillatory motion in machinery that requires repetitive, back-and-forth movement. From robotic arms to wind turbine pitch bearings, these specialized bearing solutions enhance performance, reduce wear, and extend lifetime by minimizing false brinelling and optimizing used grease distribution.
Traditional steel balls often struggle in oscillating applications due to issues such as localized surface damage, insufficient lubricant film, and premature fatigue. Hybrid oscillating bearings, which combine steel rings with ceramic elements, offer a successful solution that significantly improves bearing life, reduces downtime, and lowers maintenance costs.
The Challenge of Oscillating Motion in Bearings
Unlike continuously rotating rollers, oscillating bearings experience one-way back-and-forth movement, which can increase the risk of false brinelling and surface fatigue. This issue arises when bearings remain stationary under load while experiencing micro-motion, leading to indentations on the raceways and premature failure.
Common examples of oscillating applications include:
- Bag welding machines, where bearings accommodate hinge-like motion
- Assembly line robotics, which require precise and controlled oscillatory motion.
- Heavy-duty industrial mechanisms, such as mining and construction machinery, where components experience frequent directional changes.
These systems demand bearings with exceptional hardness, optimized geometry, and superior surface protection to withstand extreme load conditions and maintain a long lifetime
Hybrid Bearings with Ceramic Balls: A Superior Solution
The Role of Ceramic Balls
Traditional steel balls in bearings are prone to surface wear, corrosion, and high friction, especially in oscillating applications where minor movement can cause surface indentation. Hybrid bearings, which combine steel rings with ceramic balls, address these issues effectively.
Key advantages of ceramic balls:
- Increased Hardness: Ceramic balls have a higher hardness than steel, reducing wear and extending bearing life.
- Superior Corrosion Resistance: Unlike steel, ceramic materials are inherently resistant to corrosion, making them ideal for harsh environments.
- Lower Friction and Temperature Resistance: Ceramic balls generate less heat, preserving used grease and ensuring a stable lubricant film.
These characteristics make hybrid oscillating bearings an important part of modern systems requiring durable and maintenance-free solutions.
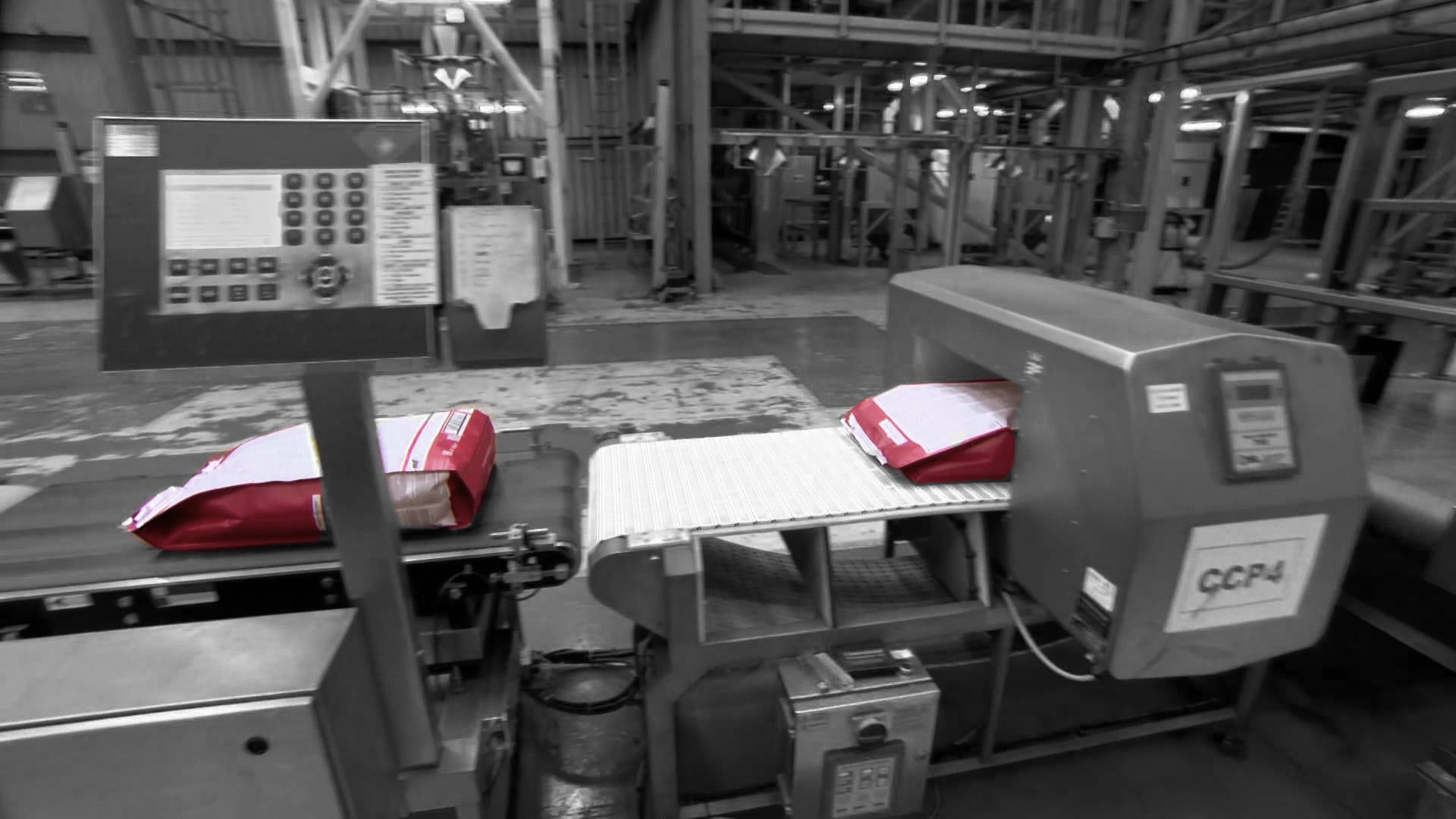
Case Study: 44x Longer Bearing Life in a Bag Welding Machine
In a bag welding machine, bearings were exposed to high-load oscillating motion, leading to premature wear, false brinelling, and surface fatigue. These challenges caused frequent failures and increased maintenance costs. By replacing standard bearings with CeramicSpeed hybrid ball bearings, the company extended bearing life by 44 times, significantly reducing downtime and production interruptions. The improved load distribution minimized surface wear, while lower operating temperatures ensured stable lubrication and prolonged grease life.
Read the full case study here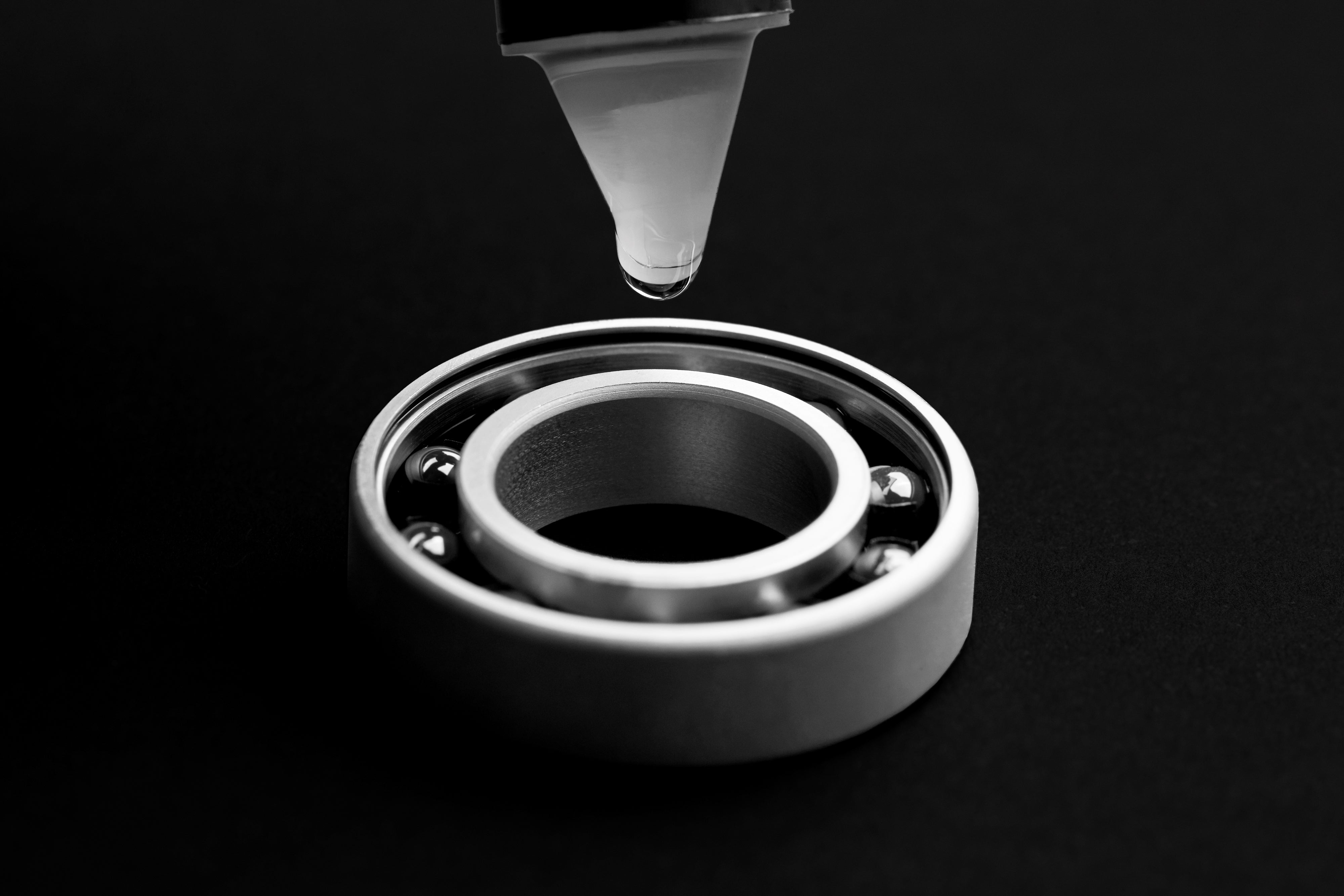
The Importance of Proper Lubrication
False brinelling is a common failure mode in bearings where the bearing experiences small movement under load. Unlike normal rolling motion, which evenly distributes wear, false brinelling causes localized damage to the raceways, leading to premature failure.
Factors contributing to false brinelling:
- Insufficient Lubricant Film: A thin or broken-down lubricant film fails to protect the bearing surfaces.
- Inadequate Grease Distribution: Poorly distributesd grease leads to increased wear and friction.
- High Loads and Vibrations: Stationary bearings subjected to continuous micro-motion experience excessive wear.
Lubrication Approaches to Prevent False Brinelling
To extend the lifetime of oscillating bearings, proper grease selection and distribution are important. High-quality lubricant with strong film-forming properties reduces the risk of wear and corrosion, while specialized bearing designs ensure even grease distributes across the raceways.
Key lubrication approaches include:
- High-performance grease formulations that maintain consistency under fluctuating temperature and load.
- Regular lubricant analysis to detect degradation before failure.
- Advanced bearing design that minimizes stagnant grease zones, allowing for continuous lubrication in oscillating applications.
Conclusion: Why Hybrid Bearings Are the Future
Hybrid ball bearings represent a transformative advancement in bearing technology, offering unmatched lifetime, wear resistance, and performance across multiple industries. By integrating ceramic balls, optimized raceways, and advanced lubricant technologies, these bearings provide a successful solution for applications requiring high durability and reliability.
Key takeaways from this article:
- Hybrid ball bearings are crucial for industrial mechanisms requiring controlled oscillatory motion.
- False brinelling and surface fatigue can be mitigated through proper lubrication and advanced bearing design.
- Hybrid solutions with ceramic balls enhance bearing life, reduce wear, and ensure optimal performance under heavy load conditions.
- Real-world examples, like the bag welding machine, demonstrate the value of successful hybrid bearing approaches.
By leveraging cutting-edge materials and innovative design, CeramicSpeed continues to set new standards in oscillating applications, providing important and successful solutions for a wide range of industries.