Vacuum Bearings for High-Precision Applications
In the world of space exploration, deep space missions, and other ultra-high vacuum (UHV) applications, selecting the right bearing system is crucial to ensuring reliability and durability under some of the most extreme environmental conditions known. Ultra high Vacuum bearings play a pivotal role in ensuring the proper functionality of equipment subjected to extreme temperature fluctuations, vacuum environments, and significant mechanical forces. Bearings must be engineered to withstand these challenging conditions without failure, as replacement or maintenance in space is almost impossible.
Why Vacuum Bearings Are Essential in Space
For a bearing to be certified for use in spacecraft, high vacuum environment or other extreme environments, it must have several key attributes. It must be able to operate in the absolute vacuum of space, where there is no atmospheric pressure. Additionally, it needs to maintain optimal performance under extreme conditions, including high and low temperatures, high G-forces during rocket launches, and the stresses of prolonged use in harsh environments. Hybrid Bearings from CeramicSpeed are bearings specifically designed and optimized to meet these demands.
The Advantages of Silicon Nitride Ceramic Balls
One of the key innovations in this field is the use of ceramic balls in hybrid bearings. Today you can find ceramic balls produced from many different ceramic material combinations. CeramicSpeed Bearings have developed a range of ultra-high bearings for vacuum applications that are engineered with silicon nitride (Si3N4) ceramic balls, which offer numerous advantages over traditional steel bearings. These ceramic balls are highly resistant to both temperature and wear, making them ideal for use in vacuum environments where temperature fluctuations are significant. The thermal expansion coefficient of silicon nitride is much lower than that of steel, which means that the bearings can maintain consistent preload and clearance control, even in the rapidly changing thermal environments found in space.
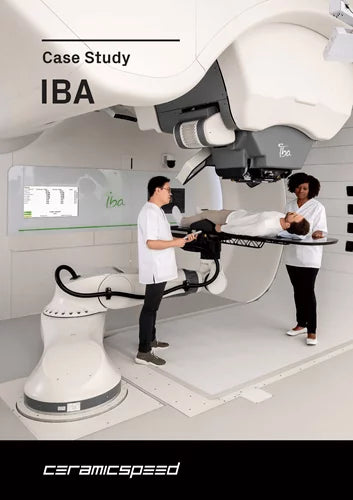
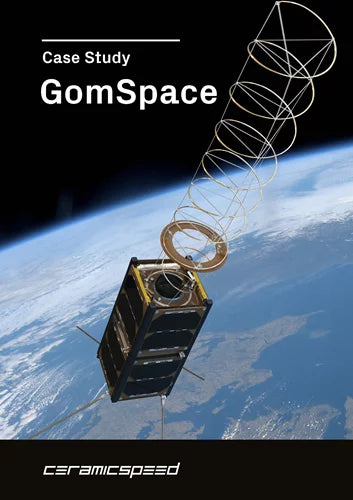
Through the course of three years, we have tested a series of material combinations and designs that have now converged into a customized ceramic hybrid bearing solution, specially designed to answer the challenges of aerospace technology.
Read the entire case hereLear how we have customized ball bearings to operate in a fierce environment with combined influence of vacuum, high temperatures, high rotational speed and high radio frequency field bringing high voltage in the system.
Read the case hereKey Insights on Vacuum Bearings
Vacuum bearings are a critical solution for applications where traditional lubricants can't be used, such as in vacuum chambers, cleanrooms, and high-temperature environments. Made from advanced materials like ceramic, silicon nitride, and stainless steel, these bearings are engineered to withstand extreme conditions and maintain optimal performance even without standard lubrication.
At CeramicSpeed, our vacuum bearings are designed for durability and reliability, with minimal maintenance needs. Whether you're facing high temperatures or contamination risks, our bearings ensure long-lasting service life.
What are vacuum bearings?
Vacuum bearings are specialized bearings designed to operate in high vacuum environments
where traditional lubricants can't be used.
What are vacuum bearings used for?
Vacuum bearings are used in environments where traditional lubricants cannot be used, such as vacuum chambers, cleanrooms, and high-temperature applications.
What materials are vacuum bearings made from?
Vacuum bearings are typically made from materials like ceramic, silicon nitride, and stainless
steel, which can operate without traditional lubrication.
Can vacuum bearings withstand high temperatures?
Yes, certain vacuum bearings are designed to withstand high temperatures, depending on the
materials and coatings used.
What maintenance do vacuum bearings require?
Vacuum bearings require minimal maintenance but should be inspected regularly for wear and
contamination. Some may need periodic relubrication with vacuum-compatible lubricants.
How do vacuum bearings differ from regular bearings?
Vacuum bearings are designed to operate in vacuum environments without traditional lubricants
and are made from materials that can withstand extreme conditions, such as high temperatures
and corrosive environments.
Performance Under Pressure: G-Forces and Temperature Fluctuations
In ultra-high vacuum applications, even small temperature changes can cause material expansion or contraction, impacting bearing performance. Silicon nitride's low thermal expansion keeps high-temperature characteristics stable, which is essential for the service life of bearings.
Silicon nitride’s 60% lower density than steel significantly reduces inertial forces during rocket launches, minimizing damage to the bearings. This makes ceramic materials ideal for withstanding G-forces and protecting the bearings from potential damage before operation begins.
Lubrication Challenges in High Vacuum Environments
In addition to their lower density and thermal stability, silicon nitride balls offer another significant advantage: improved wear resistance. In space, liquid lubrication is difficult to use effectively due to the lack of atmospheric pressure. Most lubricants that work well in Earth’s atmosphere either evaporate or degrade in a vacuum, rendering them ineffective. Vacuum-compatible liquid lubricants do exist, but they are rare, expensive, and still pose a certain level of risk due to their limited performance in extreme conditions.
Hybrid Bearings: Combining Steel and Ceramic for Maximum Efficiency
This is where hybrid bearings- which combine steel and ceramic materials - offer a unique solution. In cases where lubrication is insufficient or completely absent, hybrid bearings excel. The friction coefficient between steel and silicon nitride is much lower than that between steel-to-steel, which means that dry contact situations create less friction. This reduction in friction is crucial in vacuum-compatible applications, as it significantly reduces wear, even in conditions where only a very thin film of lubrication is present. Moreover, the risk of micro-welding - a phenomenon where metal-to-metal contact causes small areas of the bearing to fuse together - is virtually eliminated when using ceramic balls in combination with steel rings.
High Temperature Characteristics: How Bearings Survive in Space
When bearings are exposed to high-temperature environments, such as those found in space, the materials used in their construction need to be highly resistant to both thermal expansion and degradation. Stainless steel, which is often used in the ring material of hybrid bearings, offers high resistance to corrosion and can withstand the rigors of extreme environments. However, when paired with silicon nitride, the performance of the bearing is greatly enhanced. Nitrogen-enriched stainless steel is another material option that offers improved wear resistance and can further extend the life of the bearing in challenging conditions.
The Importance of Material Compatibility in Ultra-High Vacuum Applications
In ultra-high vacuum and high-temperature applications, the strict compatibility of materials is essential. The materials used in the bearings must have low vapor pressures to prevent outgassing, which can compromise the vacuum environment. Ensuring material quality is therefore critical in the manufacturing process of bearings for vacuum applications or high temperature bearings. By selecting optimized materials and high-grade stainless steel, CeramicSpeed Bearings ensures that their products can withstand the harshest conditions without compromising performance.
Applications Beyond Space: Precision Bearings for High Vacuum Use
The role of vacuum bearings is not limited to space applications alone. These advanced bearing systems are also crucial in other vacuum-compatible environments, such as in thermal mass flow controllers, multi-stage mechanical goniometers, and other precision instruments that operate in high vacuum or ultra-high vacuum conditions. In these applications, where precise movement and control are required, ball material quality and ring material composition are of utmost importance. Bearings need to be meticulously designed to reduce friction and wear while maintaining high levels of performance over time.
Advanced Vacuum-Compatible Bearings: Optimized for Reliability
One of the standout features of CeramicSpeed Bearings is the performance and lifetime characteristics of their products. Because their bearings are designed with high temperature-resistant and vacuum-compatible materials, they can function for extended periods, even under the most demanding conditions. The high-temperature characteristics of their bearings ensure that they can operate effectively in both high-temperature and low-temperature environments, which are often encountered in space and vacuum applications.
Ensuring Material Quality and Compatibility
Moreover, the market stock availability of CeramicSpeed Bearings ensures that engineers and designers have access to high-performance vacuum-compatible bearings when they need them. Comprehensive material reports accompany their products, providing detailed information on the material composition, testing, and certification of each bearing, ensuring that users have confidence in the quality and reliability of the product.
The Future of Vacuum Bearings: Innovation and Availability
In conclusion, the development of proprietary vacuum-compatible bearings represents a significant advancement in bearing technology. By combining the best properties of ceramic balls, nitrogen-enriched stainless steel, and vacuum-compatible liquid lubricants, CeramicSpeed Bearings provides a solution that is capable of withstanding the harshest conditions found in high vacuum and ultra-high vacuum environments. Whether for space exploration, deep space missions, or other precision applications in high vacuum environments, these bearings are specifically designed to offer unmatched performance, reliability, and long service life.